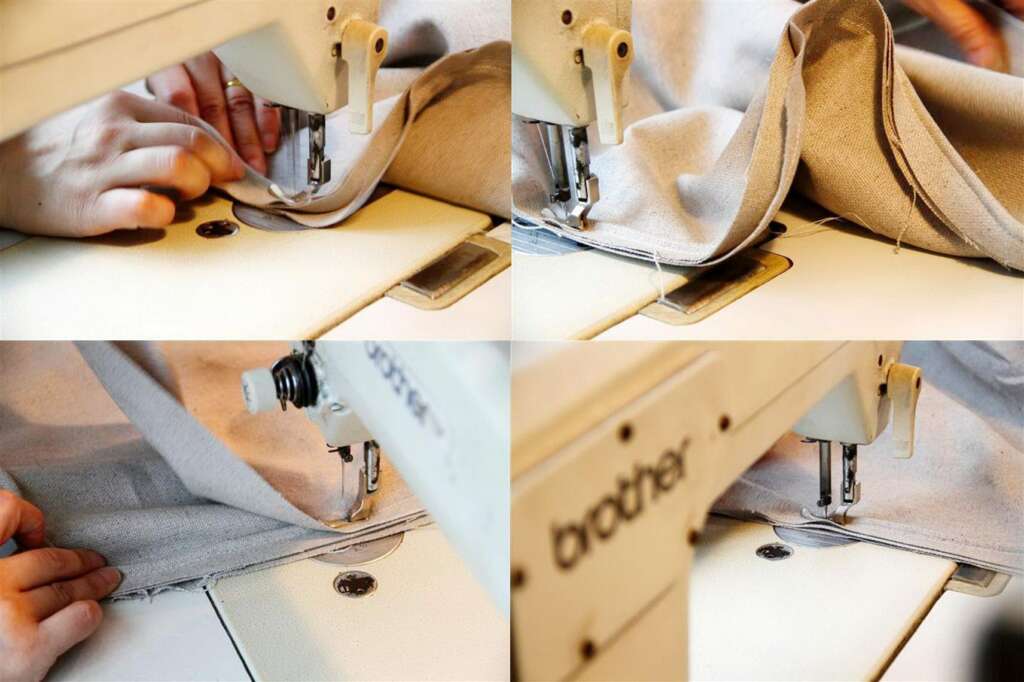
We’ve put together a behind the scene, sneak-peak in to the making of a custom Comfort Works sofa slipcover. (Note that this post is PICTURE HEAVY and may take some time to load)
Step 1: Fabric Availability
“I have just placed my order, what happens next?” Well, once an order is finalised, PayPal will issue you a confirmation. Simultaneously, Comfort Works will also send you an email, invoice attached, within 24 hours to confirm production timeline and fabric availability. While most of Comfort Works’ fabrics are stocked in house — certain popular fabrics may occasionally run low in stock and will require additional batch to be delivered from the milling house. Not to worry, we make sure that we keep our customers in the loop when the odd occasion happens.
Keep in mind also, when dealing with natural fabrics, especially naturally dyed linens and cottons, there will be slight differences from dye lot to dye lot. Lots can basically differ in shades and tone, roughly between 2-5% variation. What we can promise is that, if you place all your slipcovers in one order batch (eg: 2 sofas and an armchair) they will be made from the same dye lot.
In this section, we take you behind the scenes to learn more about the production of a Manstad Loose Fit sofa slipcover in Lino Brushed.
Step 2: Pattern Making
Once we have confirmed that there is enough fabric for your order, a fabric roll is retrieved and delivered to the cutting room. The roll is unhooked and 16 meters of fabric is set aside.
A rough skeleton of the sofa is printed out and measurements are hand drawn. It takes a well trained and highly experienced “master cutter” to be able to “imagine” how your sofa would look like, break it down into pieces and draw directly on to the cloth. This is why, if you turn our slipcovers inside out – sometimes you may spot a faint chalk line pattern ;)
Yes, we are pretty old school (who writes anything these days?!) but all Comfort Works upholsterers and seamstresses are trained to think, hand draw and match patterns in 3 dimensions, without the use of a computer! THIS is what differentiates us and makes us more flexible, enabling our team to provide you with NON-IKEA slipcovers, dining chair covers and even creating custom IKEA slipcover orders.
Step 3: Pattern Cutting
Usually pattern cutting involves creating shapes on paper templates of each section of the sofa, which is then traced and machine cut. However, as each Comfort Works’ order is made individually and requires a unique pattern to be cut, our expert panel makes creating shapes directly on your fabrics look so easy!
But in truth, Pattern Drawing and Cutting is probably the most time consuming, tedious process of creating a tailored made slipcover– as measurements must be double-checked at this stage. To make one Manstad Loose-Fit slipcover, roughly 31 pieces of cut-outs are made from the 16 meters of fabric.
Also, it takes years of experience to be able to hand cut a long straight line. Why don’t you try it, let us know how you go ;)
Step 4: Edging
Now, we get to the machines! A manual overlock machine, otherwise known as an edging machine, is used to trace the edges of all 31 pieces to create a hem or seam. As the fabric is fed through, this machine cuts the raw edges of the cloth.
The white thread creates a protective loop, so that the raw edges of fabric are contained within the seam. This technique creates crisp, neat joins between pieces (we hate frayed or loose strings) while reinforcing high-stress areas, giving you the quality finish you would expect from a tailor made slipcover.
Step 5: Stitching
Our products are carefully handmade with expert attention to detail. At this stage, the bigger pieces are now joined together.
Heavy-duty zippers are locked into place. Our non-slip lining is attached. Comfort Works tags are lovingly added to “discrete” places of your slipcover.
This is the part where us “audience” will start to see the actual “shape” of the sofa coming together.
You know…the “AH HAH!” moment.
Step 6: Piping
Long strips of fabrics are sewn as “borders” into the edges of the slipcover. This optional process is also known as piping, welting or cording.
Piping is sewn on the outer side initially, and then once more inside, to achieve a rigid look. Think of it as giving your slipcover a “spine”. Although, this takes a long time to create — trust me, it is well worth it. Wouldn’t you want the extra “grown-up” wow-ness it gives to your slipcover ?
Step 7: Skirt
As a finishing touch, the Manstad Loose-fit slipcover comes with BOX PLEATs on all four corners of the slipcover. This pleat essentially joins 2 different knife pleats together to create that tailored look, commonly seen in draperies.
Personally, I think piping and skirts gives your sofa slipcovers more personality. You can have a basic straight skirt if you like your sofa with nice clean lines. Or you can add knife pleats or ruffles if you are feeling fancy.
Step 8: Trimming Excess
At this stage, the covers would normally have its loose threads cut. This may seem like an easy task but its not something we take for granted.
Step 9: Fitting , Tweaking
As you can see, the Loose Fit would require you “split” your Manstad in half ;) Here, the slipcovers go through Quality Control checks for zippers, sizing etc. Other necessary tweaks are also done at this stage.
Step 10: Iron and Pack, Ship
The final ironing, cleaning and packing of slipcovers. The slipcovers are then boxed and shipped straight to your waiting living space! Hopefully, this paints a bit more a clearer picture of what happens after they put an order through to our webstore.
It’s a good idea to double check your PayPal mailing address, as that’s the address we will mail your covers too. Below is what the end results look like.
You can now buy the Manstad Loose-Fit slipcovers via our website. Click on this LINK.